Introduce the basic functions and importance of air pressure reducing valves
Air pressure reducing valve is an important industrial equipment, mainly used to regulate and stabilize the gas pressure in the system. This valve converts high-pressure gas into low-pressure gas suitable for a variety of industrial applications. In the fields of industrial production, medical treatment, scientific research and other fields, air pressure reducing valves ensure the safe operation of equipment, improve work efficiency and reduce energy consumption.
First, the basic function of a pressure reducing valve is to protect downstream equipment from high pressure damage. By automatically adjusting pressure, the pressure reducing valve ensures that gas is supplied at a constant pressure, avoiding equipment failures and safety accidents caused by pressure fluctuations. In addition, the pressure reducing valve can effectively control the flow rate, making the use of gas more efficient and economical.
Secondly, the air pressure reducing valve plays a key role in improving the overall stability and reliability of the system. They enable the entire air supply system to run smoothly, reducing maintenance costs and extending equipment life. In addition, the presence of pressure reducing valves is also crucial to comply with environmental standards and regulations, as they help reduce energy waste and harmful gas emissions.
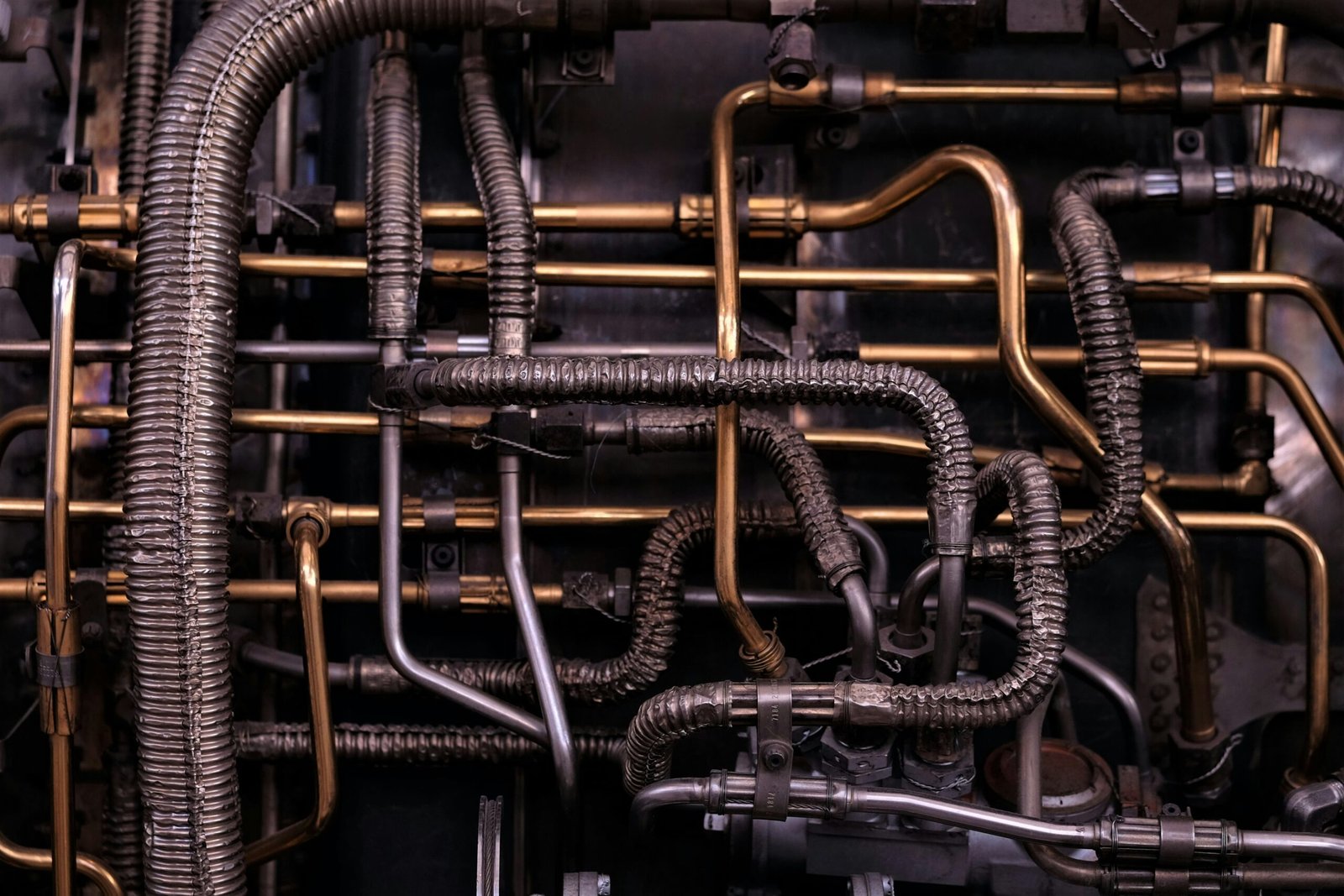
How the air pressure reducing valve works
How an air pressure reducing valve works involves two key steps: controlling air flow and regulating pressure. These steps ensure gas flows through the system at a preset safe pressure, protecting downstream equipment and enabling precise flow control.
The flow of air through the pressure reducing valve
- Inlet pressure: High-pressure air first enters the inlet end of the pressure reducing valve.
- Valve Adjustment: When air enters the valve body, it encounters an adjustable valve or valve core. The opening of this valve can be adjusted as needed to allow a certain amount of gas to pass through.
- Pressure Regulation Zone: The gas passing through the valve then enters a specific zone where the pressure is reduced to the desired level.
- Outlet pressure: The regulated gas flows out through the outlet of the valve body and is supplied to downstream equipment.
Mechanisms to control stress
The key mechanisms for controlling pressure are the diaphragm (or diaphragm) and spring within the valve. How these components work together:
- The role of the diaphragm: The diaphragm is a sensitive component that can elastically deform according to pressure changes. When the pressure on the downstream side (outlet side) is too high, the diaphragm senses this pressure change.
- Spring adjustment: The diaphragm is connected to a spring, which presets a pressure point. The deformation of the diaphragm acts on the spring through the mechanical connecting rod to adjust the opening degree of the valve.
- Feedback adjustment: If the outlet pressure exceeds the set value, the deformation of the diaphragm increases, causing the spring connected to it to compress, which in turn causes the valve to partially close and reduce the gas flow until the pressure drops to the set range. On the contrary, if the outlet pressure is lower than the set value, the diaphragm deformation decreases and the spring expands, further opening the valve and increasing the gas flow.
Types and selection of air pressure reducing valves
Selection of air pressure reducing valves involves considering a variety of types and configurations to meet specific application needs. Understanding the different types of pressure reducing valves and their characteristics can help users make a more appropriate choice.
Main types of air pressure reducing valves
Single stage pressure reducing valve:
- Single-stage pressure reducing valves have a pressure reducing stage and are suitable for applications with small pressure fluctuations.
- They are generally simpler and more economical and suitable for situations where ultra-high precision control is not required.
Two-stage pressure reducing valve:
- Dual-stage pressure reducing valves contain two stages of pressure reduction and can handle high differential pressures and large pressure fluctuations more efficiently.
- This type of pressure reducing valve provides a more stable output pressure and is suitable for complex applications requiring high-precision pressure control.
Pressure reducing valves with special materials:
- For special industrial environments, such as corrosive gases or extreme temperatures, pressure reducing valves made of corrosion-resistant materials or high-temperature materials are selected.
How to choose the right air pressure reducing valve
When choosing the right air pressure reducing valve, you should consider the following key factors:
- Input and output pressure requirements: Select the appropriate pressure reducing valve type based on the system’s maximum input pressure and required output pressure range.
- Flow requirements: Determine the maximum flow required and select a pressure reducing valve that can meet this flow requirement.
- Operating environment: Consider the operating environment the pressure reducing valve will face, such as temperature, humidity and potential chemical exposure, and select appropriate materials and design.
- Installation space and ease of maintenance: Consider the installation space on site and convenience requirements for maintenance.
- Budget and cost-effectiveness: Weigh the cost-effectiveness of different types and brands, considering budget constraints and long-term running costs.
Comparison of single-stage and double-stage pressure reducing valves
Single-stage and double-stage pressure reducing valves are two common types of pressure reducing valves, each with its own characteristics and best application scenarios. Understanding the differences between these two types can help you choose a more appropriate pressure reducing valve based on specific operating conditions and needs.
Single stage pressure reducing valve
Single-stage pressure reducing valves contain one pressure reducing stage. They are simple in design, low in cost, and suitable for applications where the inlet pressure is relatively stable. The following are the main features of single-stage pressure reducing valves:
- Simplicity: simple structure and easy maintenance.
- Cost-Effectiveness: Relatively low manufacturing and purchase costs.
- Scope of application: Suitable for environments with small pressure fluctuations, such as household or small industrial applications.
- Limitations: In environments with large pressure fluctuations, the output pressure may not be stable enough and easily affected by changes in inlet pressure.
Two-stage pressure reducing valve
Dual-stage pressure reducing valves feature two consecutive stages of pressure reduction and are able to handle high differential pressures and large pressure fluctuations more efficiently. The following are the main features of a two-stage pressure reducing valve:
- High stability: Through two-stage pressure reduction, the stability of the output pressure is significantly improved, especially when the input pressure fluctuates greatly.
- Scope of application: Suitable for demanding industrial applications, such as laboratory equipment or precision manufacturing, where extremely stable pressure is required.
- Cost: More expensive than a single-stage pressure reducing valve, and the structure is more complex.
- Maintenance needs: More frequent maintenance and inspections may be required due to the more complex internal structure.
Select suggestions
- Budget and cost considerations: If the budget is limited and the application scenario does not require high pressure accuracy, a single-stage pressure reducing valve is an economical and practical choice.
- Pressure stability requirements of the application: For those applications that require very stable pressure output, such as scientific research and precision processes, it is recommended to use a two-stage pressure reducing valve.
- Environmental changes: In situations where environmental conditions or input pressure change frequently, a two-stage pressure reducing valve can provide better performance.
How to choose the appropriate pressure reducing valve according to different needs
Selecting the appropriate air pressure reducing valve needs to be determined based on specific application requirements, working environment and technical parameters. Here are some key factors and steps to help users make an informed choice:
1. Assess stress needs
- Inlet pressure: Knowing the maximum inlet pressure of the system is the first step in selecting a pressure reducing valve to ensure that the pressure reducing valve can withstand the maximum pressure.
- Outlet pressure: Determine the required outlet pressure range and select a pressure reducing valve that can provide the corresponding adjustment range.
2. Determine traffic requirements
- Maximum flow: Consider the maximum gas flow required in the system to ensure that the pressure reducing valve can operate normally and the pressure is stable under this flow.
- Flow adjustment: Choose a pressure reducing valve that can finely adjust the flow to adapt to different working conditions and needs.
3. Consider application scenarios
- Industrial, medical or laboratory: Different application scenarios may require special pressure reducing valve characteristics, such as higher accuracy or corrosion-resistant materials.
- Environmental conditions: Environments with high temperature, high humidity or corrosive gases require specific types of pressure reducing valves, such as stainless steel or special alloy materials.
4. Select pressure reducing valve type
- Single or dual stage: Choose the appropriate type based on pressure stability needs. If pressure fluctuations are large or very precise pressure control is required, a two-stage pressure reducing valve should be selected.
- Special functions: If quick release or special safety requirements are required, choose a pressure reducing valve with these functions.
5. Installation and maintenance considerations
- Installation space: Consider the size and installation space of the pressure reducing valve to ensure there is sufficient space for installation and future maintenance.
- Maintenance needs: Evaluate the ease of maintenance of the pressure reducing valve and select a design that allows easy maintenance and replacement of parts.
6. Budget and cost-effectiveness
- Initial investment and operating costs: Weigh the initial purchase cost and long-term operation and maintenance costs, and choose a cost-effective pressure reducing valve.
Applications
Air pressure reducing valves are widely used and vital in industrial, medical and scientific research fields. The following are specific application examples of air pressure reducing valves in these three areas, showing how they meet various specific needs:
Industrial applications
In industrial production, air pressure reducing valves are used in a variety of systems and equipment to ensure that gas pressure is controlled at a safe and effective level. For example:
- Pneumatic control system: In automated production lines, pressure reducing valves are used to regulate and control the pressure of pneumatic motors and cylinders.
- Spraying equipment: In the coating process, accurate pressure control is very important to ensure the uniformity and quality of the coating.
- Air Compressor: Pressure reducing valves are used to protect air compressors and other equipment from pressure fluctuations.
Medical field applications
In the medical industry, the importance of pressure reducing valves is reflected in their precise control of gas supply, especially when dealing with life-critical gases:
- Respiratory equipment: Pressure reducing valves are used to regulate the pressure of oxygen and other medical gases delivered to patients to ensure safe and appropriate respiratory support.
- Anesthesia equipment: During surgery, pressure reducing valves are used to precisely control the flow and pressure of anesthetic agents to ensure patient safety.
- Laboratory gas supply: Medical laboratories use pressure reducing valves to ensure the accurate ratio and pressure of various gases used in experiments.
Application in scientific research field
The demand for pressure reducing valves in the scientific research field places special emphasis on accuracy and reliability, because the accuracy of experiments directly affects the validity of research results:
- Laboratory gas control: In chemical and physical experiments, pressure reducing valves are used to accurately control the pressure of rare gases and reaction gases used in experiments.
- High-precision instruments: Many high-precision scientific research instruments, such as mass spectrometers and electron microscopes, require a stable gas environment, and pressure reducing valves play a key role in this.
- Environmental simulation: Scientific research often requires simulating different environmental conditions. Pressure reducing valves help create and maintain the required air pressure conditions in closed systems.
In summary, air pressure reducing valves play a vital role in many fields such as industry, medical and scientific research, and their accurate selection and maintenance are extremely important to ensure the safety, efficiency and stable operation of the system. Selecting a suitable pressure reducing valve requires consideration of multiple factors such as the application environment, pressure and flow requirements, and proper maintenance ensures the long-term performance and reliability of the pressure reducing valve. By precisely controlling gas pressure, pressure reducing valves help improve operating efficiency, extend equipment life and comply with safety standards. Therefore, understanding the function of a pressure reducing valve, selecting the appropriate type, and performing regular maintenance are integral parts of the design and operation of any system that relies on precise air pressure control.